100+ forklifts for JJ Foodservice
JUNGHEINRICH SUPPLIED the MHE, including counterbalances, pallet movers and reach trucks to the restaurant supplier.
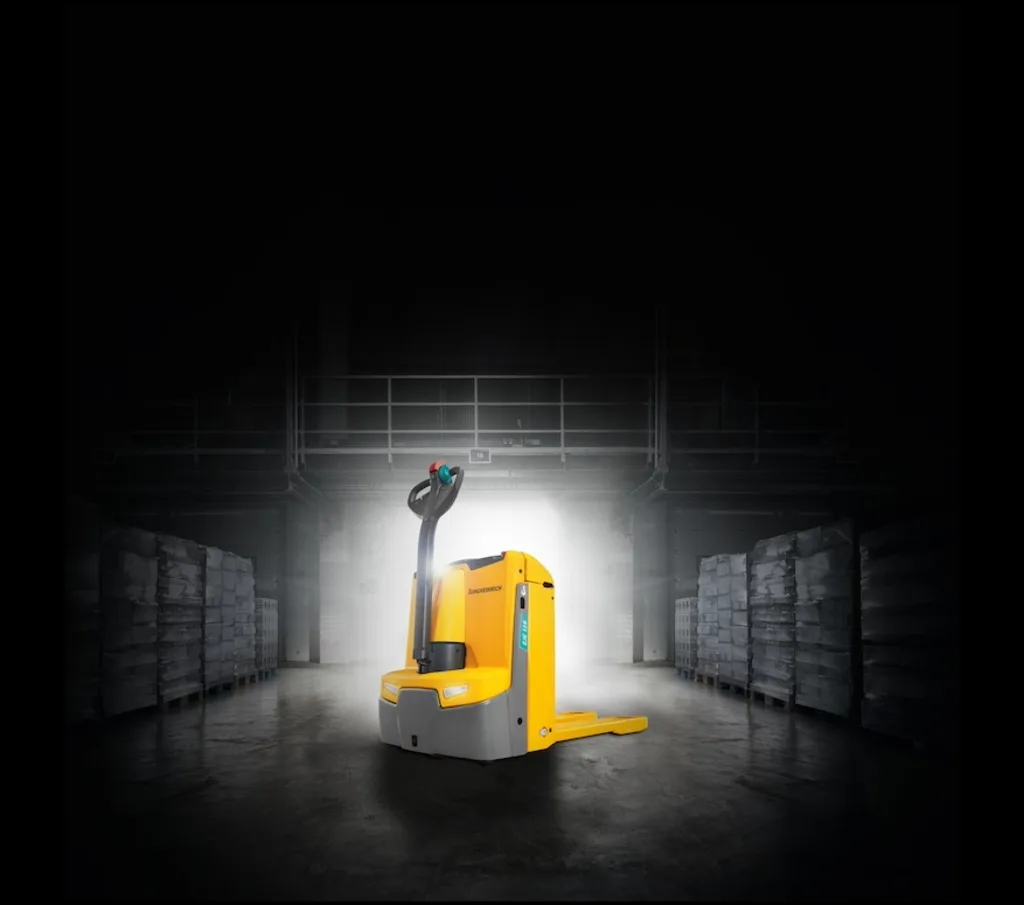
Operating from 12 branches across the UK, JJ Foodservice switched to Jungheinrich as MHE supplier. JJ Foodservice chief operating officer Kaan Hendekli, says: “Every organisation needs to change; you can’t stand still. And you need a partner who can support you in doing that. Jungheinrich visited every single branch to identify the specific needs of each site.”
Jungheinrich UK key accounts manager Tom Gelderd, adds: “JJ Foodservice was using a mix of gas and electric trucks. Reducing the fleet’s carbon footprint and optimising operational costs were key priorities, but logistics and health and safety were also big drivers of change.
“The existing fleet of MHE had been powered by 200+ batteries and the previous supplier had not explored battery change systems. The operations team were required to manually change batteries on a roller bed system. This is a common solution in the UK, however on a reach truck, where a battery can weigh the best part of a tonne, this is physically exerting and comes with H&S concerns, fatigue and logistical challenges. There was a clear opportunity to explore other solutions and work with JJ Foodservice to operate more efficiently.”
Each truck now uses just one battery, which simply plugs in and recharges when drivers take breaks. “This saves time, because there’s no longer a need for battery changeovers,” explains Tom. “It also reduces operational costs because they only need half the number of batteries. Space where the battery change roller beds were located has now been made available and JJs have been able to store pallets in some of these areas. And there’s the health and safety aspect that comes from no longer needing to change batteries.”
Transition
Replacing the internal combustion engine (ICE) trucks presented, on the face of it, just as big a challenge. Unless JJ Foodservice could feel confident that its counterbalances had the necessary charging windows and charge points, they would need to remain.
Jungheinrich placed a tracker on the ICE trucks to identify charging windows and optimal locations and was able to convert to electric without disrupting any operational shift patterns.
Double-deep vision
JJ Foodservice warehouses operate a double-deep racking system. At height, this had created real challenges for forklift operators who need to be diligent to avoid racking damage. JJ Foodservice’s trucks already had cameras fitted, but it was clear that, with different lighting levels and racking heights, the trucks needed a site-specific camera fitted to each truck, tailored to each branch’s requirements.
A range of lenses, including a wide-angle lens, now give truck operators the vision they need to reduce rack and product damage at each site.
In addition to improved visibility, the narrower truck width has given a greater aisle clearance that is helping to protect valuable stock.
For more information, visit www.jungheinrich.co.uk