Automating the trailer loading process to improve employee wellbeing
Automation can significantly enhance working practices and mitigate risks while unlocking much-needed efficiencies.
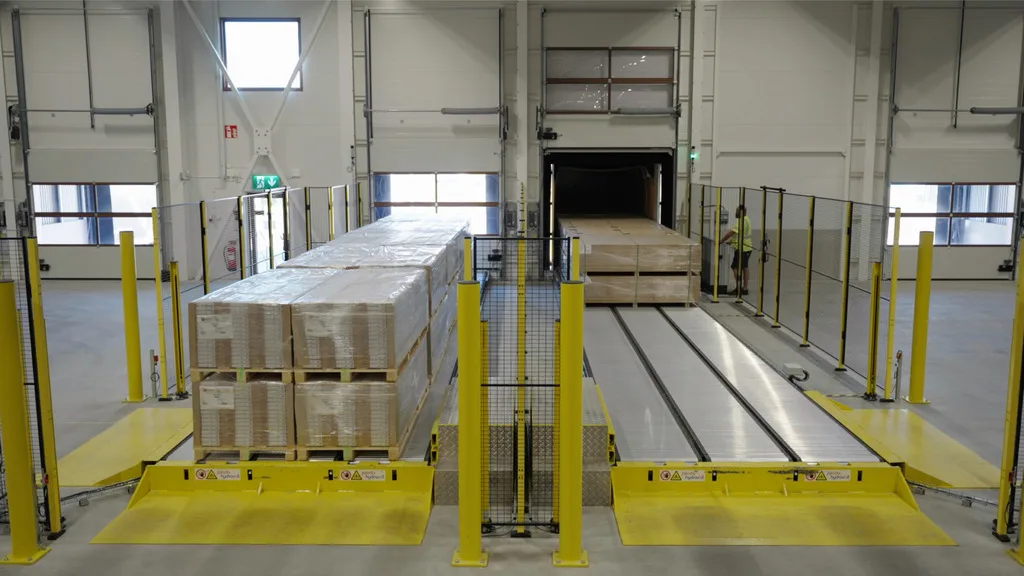
FROM WORKFORCE shortages to demand for higher velocity fulfilment to low employee retention, businesses face a web of warehousing challenges that can only be overcome by placing staff wellbeing at the same priority level as operational excellence, says Joloda Hydraroll sales director Wouter Satijn.
With a high percentage of accidents happening in or around the loading bay of a warehouse or factory, this is considered one of the more dangerous areas for businesses to address first.
By automating the loading process, it’s possible to transform employee experiences, protecting staff while increasing productivity in the following ways:
1. Avoid manual handling
Loading and unloading bays are hard places to work, with employees under pressure to meet increasingly tight deadlines. Manually unloading and loading trailers is exceptionally physically demanding for operatives, who often rely on winches and ropes to move heavy items. An automated loading system can radically reduce the amount of physical work required by employees. Rather than 45 minutes of highly physical activity for each trailer load, the job can be completed in just five minutes with automation. Heavy and dangerous items can be loaded and unloaded without manual intervention, further improving employee safety.
2. Reduce forklift traffic
Adding to safety risks in the loading bay is a reliance on forklift trucks, which are involved in a quarter of all workplace transport accidents. Automating this part of the logistics process means fewer forklift trucks are required, minimising the risk of accidents and product damage, while cutting costs and freeing up valuable space. Businesses can increase output by reducing the storage space in the loading area, and staff have more opportunities to take up roles that are better paying, or that they find more enjoyable.
3. Minimise human error
Stressed workers under high-pressure deadlines are at risk of making mistakes. And, within the loading area, mistakes can be devastating. From breakages to spillages, slipped loads to vehicle creep, human error due to inexperience, lack of concentration or over-tiredness can create an array of potentially lethal hazards. The whole situation can be transformed by giving staff fail safe, automated systems that ensure the right procedures are followed at all times.
Conclusion
Automating the unloading and loading process greatly improves safety and reliability throughout the entire operation. Goods move quickly through loading areas without the need for forklift trucks. Processes are more efficient, easing the pressure on staff and ensuring deadlines are hit, even in the event of staffing challenges or peak demands. And, with the entire process requiring far fewer people, it ensures a safer, more fulfilling, and enjoyable environment for the existing workforce.
For more ways automation can improve safety in the loading bay, download the white paper from Joloda Hydraroll, here.