Distillery sees MHE fleet overhaul
THE MATERIALS Handling division of Robert Purvis Plant Hire has overhauled the forklift truck fleet at Glen Turner’s Starlaw Distillery, in Bathgate, West Lothian.
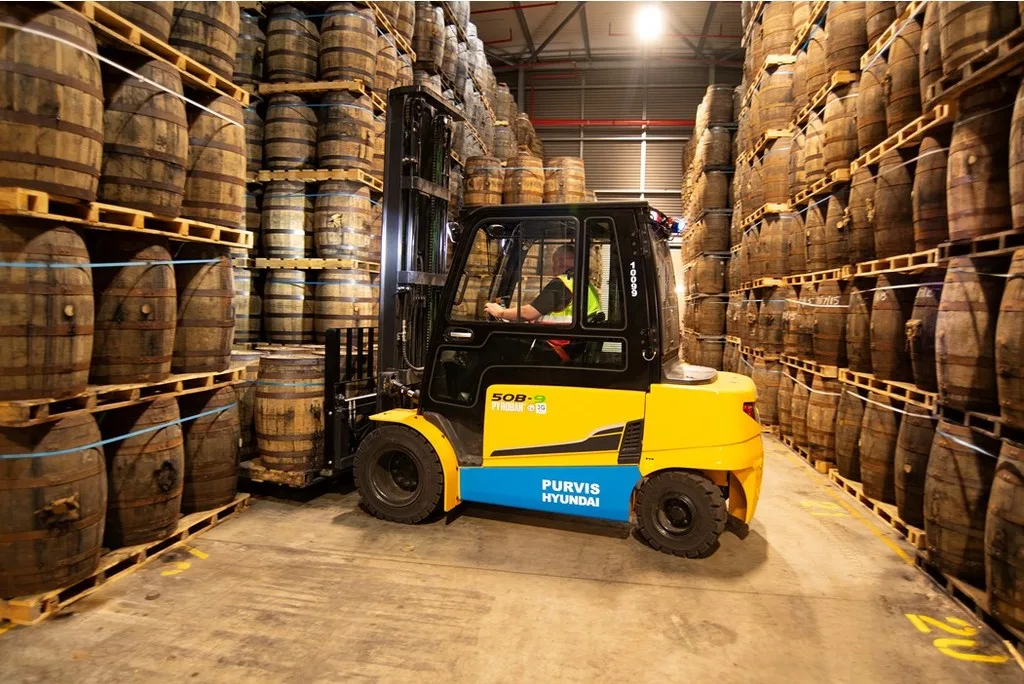
The company has provided the whisky distiller with a mix of 3.5-tonne Hyundai 35B-9U models for its dispatch warehouses and Zone 2 prepared, 5-tonne capacity, Hyundai 50B-9 forklifts for the site’s barrel storage facilities.
Ten 35B-9U forklifts have been purchased by Glen Turner, while six fire-protected 5-tonne machines have been supplied as part of a seven-year contract hire agreement. Full back-up and maintenance will be provided by Purvis for all of the machines, from its head office location in nearby Lochgelly, Fife.
Glen Turner dispatch team leader Neil Grant, says: “We were taken to see Hyundai trucks in use. They were genuinely one of the best we’ve tried.
“For feel, comfort and reliability they are the best. You also sit slightly higher, which gives a better view over the forks.”
{EMBED(1291254)}
To cope with a constantly variable workload, the 3.5-tonne forklifts have been provided with a 5.5m triple boom mast and hydraulically-adjustable, four-fork double pallet frames. These allow the operators within the distillery’s distribution centre to lift two pallets of whisky side by side, greatly increasing productivity.
Glen Turner has three main bottling lines, two producing up to 13,000 bottles an hour and one with a 7,500 bottles per hour capacity. There is a smaller fourth line, for miniatures and other limited volume products. In total, the distillery holds around 3.2 million bottles of whisky in stock at any one time.
“We’ve customised the machines by attaching a computer screen from the roof, so when we pick an order, everything is at eye level for the operator,” said Mr Grant.
The larger 5-tonne models are used to locate casks within the site’s ageing cellars, which can hold more than 750,000 casks over many years of maturation. Due to the volatile vapour that can be given off during this process, known as the ‘Angel’s share’, the 50B-9 forklifts have all been specially prepared for distillery use, with specialist supplier Pyroban installing bespoke explosion protection kits.
{EMBED(1291255)}
This ATEX 3G conversion combines Pyroban’s System6000 gas detection with explosion protection. If gas or vapour is detected above pre-set levels, the driver is given a visual and audible warning to move away from the area of potential danger. If increased levels of vapour or gas are detected the truck can automatically be safely brought to a stop, to protect the driver and the site.
The 5-tonne machines have been equipped with 7.5m lift masts, to allow them to stack up to seven casks high. They have full cabs with heaters and wide, side-shift carriages, with three aluminium-clad forks, to prevent any risk of sparks.
Purvis has provided all of the forklifts with high amp, opportunity-charging lead acid batteries, from local supplier Capitol Industrial Batteries in Cumbernauld. The company has also installed new charging facilities for all of the machines, that allow the operators to charge whenever they have the opportunity, rather than waiting for the end of a shift to plug in. That said, the 3.5-tonne forklifts are easily managing two shifts on a single battery charge within the distribution centre.
{EMBED(1291256)}
“The back-up from Purvis and Hyundai has been phenomenal,” said Mr Grant. “Any time we phone or e-mail, within 24 hours everything is done, it’s fixed and back on the road. We don’t have any downtime for the Hyundais at all.”
For the first time in an operation of this type, all of the forklifts have been equipped with HD Hyundai’s HiMate machine monitoring system. This provides individual operators with access codes, that then lead them through their daily checks on the machines. The system can be used to zone manage operation, shutting down forklifts if they are operating in the wrong area. It also flags up servicing and maintenance requirements as needed.
“HiMate is a very clever system. It gives everyone their own ID,” said Mr Grant. “There’s a log-in process for health and safety and everything has to be working and checked for the truck to work. If there was a failure it would automatically send it to the supervisor and to an engineer. It’s a great fleet management system and we can keep track of everybody, all of the time.”
For more information, visit www.hyundai-mh.eu