Fashion drives new automated DC
3PL Noatum Logistics recently moved into a 500,000 sq ft distribution centre in Biggleswade, which features a turnkey automated handling solution delivered by BS Handling Systems. Richard Dannatt tells the story of how it came together.
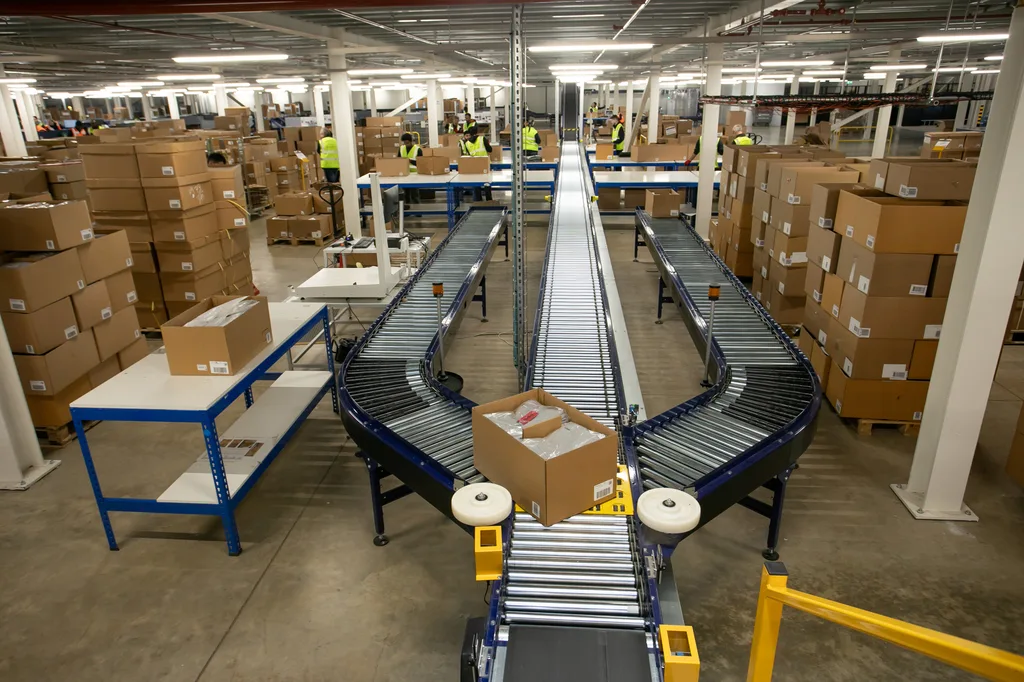
THE FACILITY has been purpose built to provide storage and distribution facilities primarily for a leading fashion retailer. In addition, it has space for Noatum to accommodate new customers as the business continues to grow.
Our key client, needed more capacity. At the same time, our business was expanding and we required space for further growth. We already had a couple of sites in the UK, the most recent being in Medway. The size and location of this new DC was ideal and so once we secured it, we began the process of selecting the right partners to develop it.
The reason we chose to work with BS Handling Systems (BSH) was essentially because they’d done a similar job for us in our Medway DC. The solution they delivered there worked very well and they proved to be flexible, knowledgeable and professional partners.
First class project management
Stephen Perriton, the project manager from BS Handling has been excellent throughout; he was with us from day one and has been alongside us throughout the design, implementation and also since go-live.
The design concepts were based our Medway site. From that point onwards, however, Stephen and the BSH team were really key in helping us to understand how the Biggleswade facility would work, and how product would move around the DC.
The fact that the whole project went so smoothly was down to the flexibility and attention to detail of BS Handling. Naturally, a site of this size and complexity goes through all kinds of variations and amendments as it develops. The BSH team understand this and always collaborated with us to ensure the final solution would accommodate both our clients and our own evolving requirements.
Three mezzanines
The site has three mezzanine floors, each 100,000 sq.ft., and working across four different levels means there is a lot of stock movement. Product comes in and goes out on the ground floor either in flat packed boxes or goods on hangars (GOH); it is then moved up the levels to be stored or picked and moved down to be despatched.
The BS Handling team was fantastic at finding the most efficient and effective way of achieving this. The semiautomated system they created integrates seamlessly with our own bespoke WMS and our third party robot systems. This means we can put goods on a conveyor (flat packed) or an overhead monorail (GOH) and they will go where they should without human interference.
Regular updates
Throughout the implementation we had regular updates with the BSH team. They were always on the ball, reporting any delays or items that might impact progress. You need to understand that there was a lot going on at the same time – the mezzanines had to be constructed, the lighting, power and sprinklers were all being installed, so there was potential for significant issues to arise if the project wasn’t handled and managed professionally.
On top of all this, our client and ourselves were making changes as the project evolved, and the BS Handling team themselves were suggesting improvements as the installation unfolded.
They were excellent at recognising elements that could be improved. When we started talking about how we would actually do things, how we would actually pick or how putting away stock would actually work, they were in these sessions with us and would listen and produce the best, practical solutions.
The materials handling experts
To a person, each BS Handling team member had a massive understanding of everything that was going on. They are true experts at what they do; they’re all very open and proactive in their thinking. Consequently, when we posed questions they would always come back with alternatives as to the best solution.
Naturally, on a project of this size, you always get the odd issue that springs up out of nowhere. On the odd occasion this happened, however, they resolved the issue very quickly.
The systems they designed and installed have proven to be the most efficient way of moving product around the warehouse. They also designed and supplied a couple of bespoke pieces of kit for us. The first is a solution that produces and automatically inserts the paperwork needed for each order requiring value added services (VAS). So, rather than having printers on each of the value added services’ desks, we just have one printer/inserter for all the orders.
The other bespoke item is a label printer which automatically applies the shipping label to the top of each box before it goes to the despatch area. The machine also folds the label over the edge of the box so it can be read from both the top and side elevations.
The product journey through the DC
On the ground floor, goods are unloaded from trailers via telescopic booms which reach into the trailers – two for flat packed products, one for GOH using the overhead monorail system.
The cartons are then manually de-lidded and go straight onto the powered conveyor system (totalling some 1200 metres). Next they have a unique identifying barcode label automatically applied to each side of the box, before travelling through a dimension, weighing and scanning station.
This information is sent via the warehouse conveyor system (WCS) to the client’s warehouse management system (WMS) to determine if the carton can go straight into storage or if it requires further manual checking.
{EMBED(1279347)}
The conveyor system takes boxed goods in up to the second or third floor where there are some 3,356 bays of shelving (a total of 29,137 linear metres). On each of the two shelving storage floors there are six off-load/on-load stations. Goods are put away and picked by a combination of people and ‘cobots’ (robots supplied by Locus Robotics), with all systems integrating with the client’s WMS.
Once picked, the boxed goods travel back down to the ground floor on the conveyors, passing through the bespoke document insertion station before going to VAS as required. From there, all boxes pass through check weighing, automated strapping stations and the bespoke label printer/applier on their way to the final despatch sortation area.
GOH
In-bound GOH are checked manually as they come off the trailer and are then sent on ‘jets’ via the overhead monorail up to the first floor. Here they are put away in the GOH storage area comprising of 1,550 bays (9,300 linear/m). When picked, they come back down to despatch via the same overhead monorail.
To complete the scheme, BSH provided a signage and labelling package, goods lifts, cardboard waste chute/conveyor system, packing benches, trolleys and partitioning.
Conveyors and overhead monorail maximise efficiency
It is clear that without the conveyors and overhead monorail systems BS Handling Systems has designed and installed here, trying to move such large volumes of product efficiently between the four floors of the DC would be impossible.
We now have a robust and efficient storage and distribution system for our high street fashion retailer, and plenty of space to take on new clients at this semiautomated DC.
Richard Dannatt, general manager Biggleswade DC, Noatum Logistics
For more information, visit www.bshandlingsystems.com