Food security farmers and retailers – how automation can help
The UK’s ability to feed itself is back on the agenda, as British farmers protest that the new tax regime will undermine an already fragile rural economy. Could automation help to create a more viable food strategy, asks Russell Hutchinson of Daifuku.
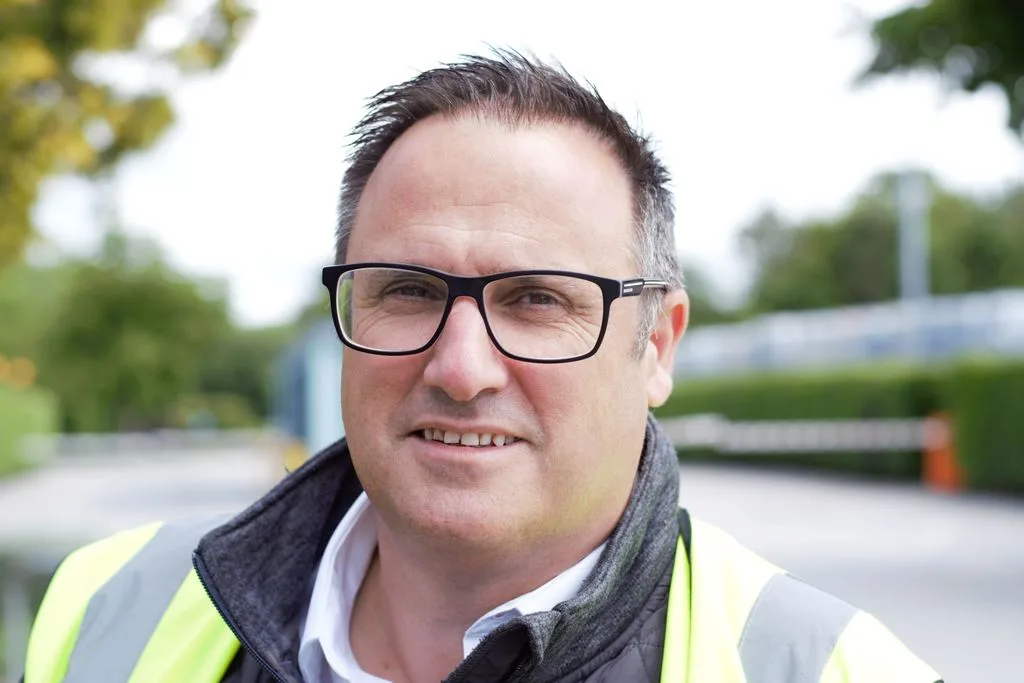
AT END of the Second World War, the UK government said food security was an issue of national importance, leading to the publication of the Agriculture Act of 1947. This legislation established a series of guaranteed payments to farmers, encouraging them to produce vital foods needed to sustain a growing population.
In late 2024, the landscape changed markedly, with the latest statistics* confirming that the UK is just 62% self-sufficient when it comes to food. To put it another way, if our country was to survive purely on the food it produced in any given year, we would be starving by mid-August. Whether it was Brexit, the end of the Common Agricultural Policy, the War in Ukraine or general global uncertainty, our ability to feed ourselves has got worse. And with the November 2024 Budget putting farmers under more fiscal pressure, this situation is likely to deteriorate further.
Pragmatic importation
Pragmatically, in order to keep supermarket shelves stocked, the UK food industry needs to consider a strategy based on importation, combined with the ability to maintain good buffer stocks of produce to iron out any peaks or troughs in supply and demand.
To achieve this, carefully targeted investment in cold chain logistics is likely to be a sound strategic move. And while home-produced goods will always play a part, the UK needs to consider the benefits of a resilient system based on overseas produce.
AS / RS and STVs to the rescue
A recurrent theme within the cold storage sector revolves around effectively accommodating an ever-growing range of goods within a restricted space. The array of frozen food SKUs and the shift toward smaller orders exacerbate the challenge of storing required volumes using traditional fixed racking and floor storage methods.
As we‘ve witnessed throughout the industry, building resiliency into the supply chain has emerged as a critical concern, further encouraging retailers to mitigate against the risks of infrastructure and environmental risks.
In the ever-evolving landscape of industrial technology, the cold chain industry is a prime example of innovation at play. With the demand for efficiency, speed, and precision rising steadily, warehouse automation has emerged as a viable solution. Among the arsenal of automation tools, automated storage and retrieval systems (AS/RS) and Sorting Transfer Vehicles (STVs) have become pivotal in revolutionising the storage processes within the cold chain industry.
Unique challenges
The cold chain industry encompasses a wide array of products, including perishable goods such as dairy, frozen foods, and fresh produce. Unlike conventional warehousing, cold food storage demands precise temperature control, stringent inventory management, and rapid order fulfilment to maintain product quality and safety standards.
Cold storage facilities serving supermarkets and restaurant chains experience high-mix, small-batch, and fast-turnover inventory. Imperative to this process is the management of goods based on expiry dates, best-before, and delivery information – a continuous flow of pallet storage, retrieval, and picking operations based on specification.
Traditionally, cold food storage facilities relied heavily on manual labour for tasks like picking, packing, and inventory management. However, this approach often led to inefficiencies, increased labour costs, and a heightened risk of errors. With the advent of automation technologies, the industry has witnessed a transformation towards more streamlined and optimised operations.
Clearly, in the UK manual labour has become more difficult, with employment costs rising and health and safety requirements placing additional burdens on food manufacturers, importers and retailers alike.
Store and retrieve
AS/RSs are a cornerstone of warehouse automation, offering unparalleled efficiency in storage and retrieval operations. These systems utilise a combination of storage racks, automated shuttles, and cranes to store and retrieve goods with precision and speed, focusing on high volume and storage efficiency.
In the context of the cold chain industry, AS/RSs offer several key advantages:
Temperature control
AS/RSs are designed to operate seamlessly within cold storage environments, ensuring that temperature-sensitive goods remain preserved throughout the storage and retrieval process.
It’s also worth pointing out that compared to a conventional cold warehouse operated by manual labour and forklifts, cold AS/RS offers better energy efficiency because it requires smaller openings for storage and retrieval, resulting in less cold air loss throughout the warehouse.
Optimised space utilisation
By utilising vertical space more effectively, AS/RSs enable cold chain warehouses to maximise storage capacity without expanding their physical footprint. This is particularly crucial in urban areas where space is limited, and land costs are high.
Enhanced inventory management
AS/RSs are equipped with advanced inventory tracking and management capabilities, allowing warehouse managers to monitor stock levels in real-time and optimise inventory rotation to minimise waste.
Automation also ensures accurate FIFO (First In, First Out) operations – an essential practice in the handling of cold and frozen foods.
Increased throughput
With automated retrieval processes, AS/RSs significantly reduce the time required to fulfil orders, improving overall throughput and customer satisfaction.
Mini Load AS/RS stores cases for a Japanese cold chain logistics provider
Sorting and moving
In addition to AS/RSs, Sorting Transfer Vehicles (STVs), a rail-guided transport system, play a vital role in enhancing the efficiency and flexibility of cold chain warehouse operations. STVs are capable of transporting goods between storage racks and picking stations with minimal human intervention.
Here are a few examples of how STVs are transforming cold food storage:
Dynamic storage access
STVs seamlessly transport goods to and from an AS/RS. The system can autonomously navigate through narrow aisles and tight spaces to deliver pallets at drop-off point where the AS/RS can retrieve them for storage. This flexibility allows for faster retrieval times and smoother workflow orchestration.
Collaborative operation
STVs can work in tandem with human operators and other automated equipment, such as robotic arms and conveyor systems, to streamline the entire order fulfilment process. This collaborative approach optimises resource utilisation and minimises bottlenecks.
Enhanced working environments
By delivering goods to operators, picking tasks can be carried out in well-lit, secure, and comfortable temperatures. This increases staff well-being and satisfaction and provides safer and more productive operations.
Scalability and modularity
STVs are inherently scalable, allowing cold chain warehouses to expand their automation capabilities incrementally as demand grows. This modular approach to automation ensures that investments remain flexible and aligned with evolving business needs.
An STV loop used by and ice cream manufacturer
Paradigm shift?
The integration of AS/RSs and STVs represents a fundamental shift in how cold food storage facilities operate. By harnessing the power of automation, these technologies empower warehouses to achieve unprecedented levels of efficiency, accuracy, and reliability.
As the cold chain industry continues to evolve in response to changing consumer demands and market dynamics, the adoption of warehouse automation will undoubtedly play a pivotal role in driving growth and competitiveness. By embracing AS/RSs and STVs, cold chain manufacturers and distributors can position themselves at the forefront of innovation, delivering fresher products faster and more efficiently than ever before.
Given the structural challenges facing UK agriculture, it looks likely that reliance on imported food will increase over the next decade. This, in turn, will require intelligent investment into efficient, scalable and reliable automation.
Operating since 1937, Daifuku has been providing logistics systems for cold storage environments to a wide range of customers since 1973. Speak to one of our specialist team as to how we assist in transforming your operations.
For more information, visit www.daifuku.com
* DEFRA 2023