Tackling uncertainty with AI
Uncertainty poses huge challenges for intralogistics. Siegfried Zwing explains how AI can help companies deal with the unexpected.
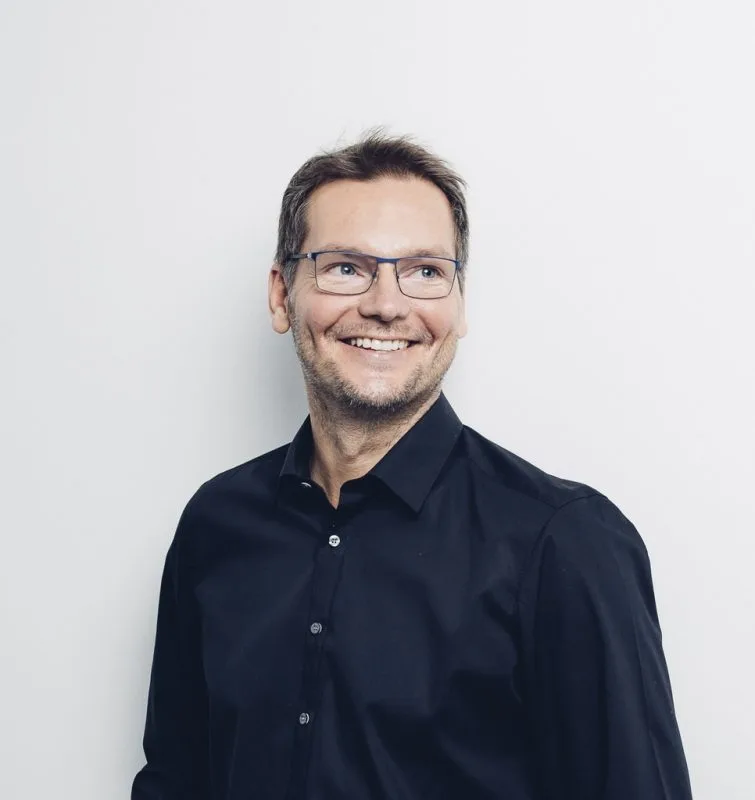
WHETHER IT’S labour shortages, material scarcity or surges in demand, uncertainty presents big problems for logistics. Artificial Intelligence is a potent means to combat uncertainty, providing agility and enabling you to build resilience for your operations. Software such as redPILOT harnesses the power of AI to help warehouse operators use available resources – such as systems, personnel, energy and materials – dynamically and intelligently in order to continuously optimise performance, despite constantly changing factors such as order structure, delivery dates and labour availability. The redPILOT solution can either be hosted as a cloud service or provided into your existing hardware infrastructure. All system experience is then used for machine learning, enabling you to make data-driven decisions and increase overall performance.
Detect bottlenecks
With redPILOT, you gain real-time intelligence in one place. The software’s teamKIOSK function tracks all warehouse activities in real-time, including those not captured by a WMS, WCS or SAP system. This data is visualised in a performance dashboard, which gives you granular, real-time and end-to-end intelligence. Both bottlenecks and excess capacity are detected via a specially developed algorithm. In this way, machine learning steadily and automatically improves your logistics operation and minimises downtime, while also detecting any hidden potential.
Improve demand forecasting
AI can enhance the accuracy of your demand forecasting. Algorithms enable expected quantities to be calculated based on historic data, growth factors and reference volumes. In this way, redPILOT helps you adapt more easily and quickly to unforeseen events and demand fluctuations.
Avoid downtime
Of course, AI also has an important role to play in minimising downtime. A CMMS (Computerised Maintenance Management System) helps avoid issues by predicting system problems and prioritising maintenance tasks. The redPILOT CMMS – which is available as a stand-alone system or as part of the complete redPILOT solution – also features a mobile app that allows technicians to access manuals, spare parts information and other service documentation.
Plan labour
Recognising that planning shift cover can be one of the most time-consuming elements of running a warehouse, redPILOT features the teamAPP for flexible labour management. This smartphone app schedules employees at optimal cost, based on required labour, employee availability and skills, as well as any customer-specific rules. The teamAPP allows employees to enter their availability, request holiday, record absence and check their shifts at any time and location. They can also request shift swaps, with all available and qualified colleagues being automatically messaged. If someone accepts the shift change without compromising performance or adding cost, the supervisor does not even need to approve it. In addition, teamApp automatically takes care of job rotation, alternating the assignment of strenuous work to help ensure all employees remain fit for work. Empowering warehouse staff in this way enhances their job satisfaction, leading to better employee retention. Using teamApp also helps reduce reliance on temporary workers, further reducing costs. Software such as redPILOT can also be used to gamify your warehouse operations, engaging and motivating your workforce through reward programmes, leaderboards or team recognition.
Unify your data
To use your data in a meaningful way, you need to break down data silos. This means unifying the data produced by the various systems – ERP, WCS, WMC, SCADA and so on – in your warehouse. By making all information available in real time and in one place, redPILOT gives you a holistic picture of your operation, helping you to identify inefficiencies, manage costs and make timely decisions. This not only makes your company more competitive but also more sustainable, which is an important factor for many consumers and employees today.
Customers enjoying the benefits of redPILOT include fashion and homeware retailer, M&S; grocery retailers, Edeka and Spar; German beverage retailer, Trinkgut; Swedish 3PL, Nowaste Logistics; and temperature-controlled logistics provider for Central and Eastern Europe, Frigologo.
Siegfried Zwing managing director, redPILOT
For more information, visit www.redpilot.com
+43 676 8979 6464