Why warehouse slotting is essential
Think slotting isn’t important? Think again. It’s an absolute essential of inventory management. Get it wrong, and you risk higher labour costs, shipping delays, and customer dissatisfaction. Learn the concept behind warehouse slotting, and get in an in-depth look at how it’s a natural feature of the AutoStore system, says Carlos Fernández.
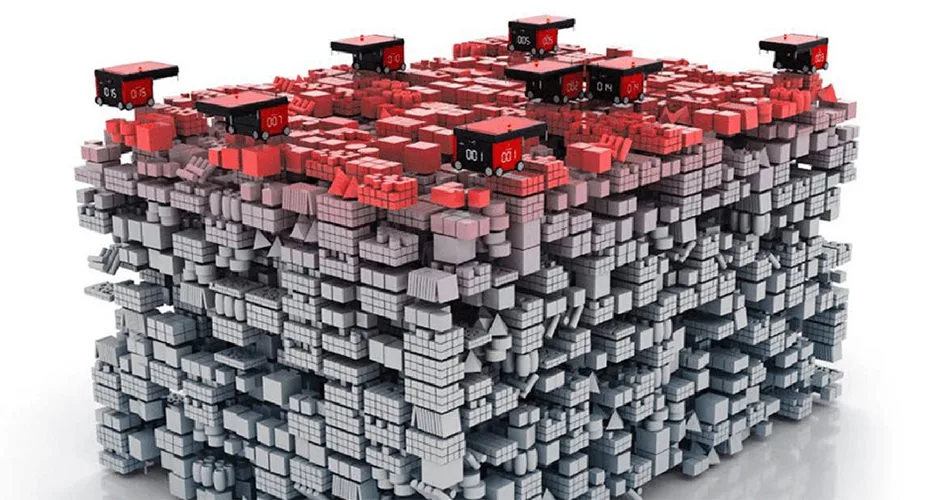
Understanding warehouse slotting
Warehouse slotting is the process of organising and placing inventory in a warehouse in a manner that optimises picking and replenishment processes. By strategically positioning items based on factors such as demand frequency, size, and weight, warehouses can significantly enhance their operational efficiency.
The fundamentals of slotting
At its core, slotting is about placing items in the most logical and efficient locations within the warehouse. This involves understanding the dynamics of inventory turnover, the physical attributes of the items, and the picking strategies employed. Effective slotting ensures that high-demand items are easily accessible, reducing the time and effort required for order fulfillment.
The role of data in slotting
Data plays a pivotal role in slotting decisions. By analysing historical sales data, order patterns, and seasonal trends, warehouse managers can make informed decisions about where to place items. Advanced data analytics and inventory management systems enable real-time adjustments, ensuring that the warehouse layout remains optimised as demand patterns shift.
Benefits of effective warehouse slotting
Implementing a well-planned slotting strategy offers numerous benefits that directly impact the bottom line and overall operational efficiency.
1. Increased picking efficiency
One of the most immediate benefits of effective slotting is increased picking efficiency. By strategically placing high-velocity items in easily accessible locations, pickers can fulfill orders faster, reducing the overall time spent on the picking process.
2. Reduced labor costs
Labor costs constitute a significant portion of warehouse expenses. Efficient slotting reduces the time and effort required for picking and replenishment tasks, leading to lower labor costs. This not only boosts profitability but also allows for better allocation of human resources.
3. Improved inventory accuracy
Accurate inventory management is crucial for avoiding stockouts and overstock situations. Proper slotting enhances inventory visibility and accuracy, ensuring that items are stored in their designated locations and minimising the risk of errors.
4. Enhanced space utilisation
Warehouse space is a valuable asset. Effective slotting maximises the use of available space by organising items in a way that minimises wasted space. This is particularly important for warehouses dealing with a wide variety of product sizes and shapes.
Understanding the benefits sets the stage for also understanding the challenges associated with slotting.
What are the risks of not slotting properly?
Effective inventory slotting is essential. Improper practices, like storing inventory randomly, can lead to several risks and inefficiencies. If you’re of the mindset that slotting isn’t important, or you want to experiment with this commonly accepted practice, consider the risks to your business:
- Increased picking time and costs: Employees may have to walk longer distances to pick inventory, slowing down the order fulfillment process and driving up costs. It can lead to multiple back-and-forth pick path (further travel distance for the robot) to fulfill different picks/tasks in an order.
- Shipping delays: Inefficiencies in picking can cause delays in order processing, resulting in unhappy customers.
- Higher risk of injuries: Poor inventory slotting increases the risk of injuries due to the need for excessive movement and handling.
- Reduced productivity: Without placing high-demand items in easily accessible locations, productivity drops and labor expenses rise.
Common challenges in warehouse slotting
While effective slotting offers significant benefits, it is not without challenges. Understanding these challenges is essential for developing strategies to mitigate them and improve overall warehouse efficiency.
Changing demand patterns
One challenge, being difficult to avoid, is the dynamic nature of demand patterns. Seasonal fluctuations, promotional events, and market trends can cause shifts in product demand, necessitating frequent adjustments to the slotting strategy. Failing to adapt to these changes can result in inefficiencies and increased operational costs.
Space constraints
Warehouses often face space constraints, making it difficult to allocate the ideal locations for all items. High-density storage requirements and a wide variety of product sizes and shapes can complicate the slotting process. Efficiently utilising available space while maintaining accessibility and order accuracy is a delicate balance.
Data accuracy
Effective slotting relies heavily on accurate and up-to-date data. Inaccurate inventory data, order records, or demand forecasts can lead to suboptimal slotting decisions. Maintaining data accuracy is crucial for ensuring that the slotting strategy remains effective.
Labour variability
The efficiency of slotting can also be impacted by labor variability. Differences in picker skills, experience, and familiarity with the warehouse layout can lead to inconsistencies in order fulfillment times. Ensuring that all employees are adequately trained and familiar with the slotting strategy is essential.
Integration with existing systems
Integrating slotting strategies with existing warehouse management systems (WMS) and inventory management software can be challenging. Ensuring seamless communication and data sharing between different systems is critical for maintaining an optimised warehouse layout.
Inventory digging
A final challenge associated with warehouse slotting is digging. This occurs when items are not organised optimally within storage containers, leading to time-consuming searches during the picking process. Digging can significantly reduce picking efficiency and increase labor costs, as employees spend more time locating items.
The good news? With properly designed technology, you don’t have to worry about this challenge. AutoStore, for example, is designed to optimise and improve the slotting process. If you don’t have this type of technology, here are some tips to ensure you get slotting right.
Overcoming challenges: Best practices and advanced solutions
To overcome the challenges mentioned above, warehouses must adopt best practices and leverage advanced solutions that enhance slotting efficiency and adaptability.
1. Analysing inventory and order data
A thorough analysis of inventory and order data is the foundation of successful slotting. This involves examining historical sales data, understanding peak seasons, and identifying high-demand items. By leveraging data analytics, warehouses can make data-driven decisions that optimise slotting.
2. Classifying inventory
Classifying inventory based on demand frequency, size, weight, and handling requirements is essential. Common classification methods include ABC analysis, where items are categorised into A, B, and C groups based on their sales volume. This helps prioritise the placement of high-demand items in prime locations.
3. Continuous training and adaptation
Ensuring that all employees are trained on the slotting strategy and familiar with the warehouse layout is critical. Regular training sessions and updates can help maintain consistency in order fulfillment and adapt to any changes in the slotting strategy.
4. Utilising slotting software & advanced automation
Advanced slotting software solutions provide warehouses with the tools to automate and optimise the slotting process. These software systems analyse data, suggest optimal locations for items, and continuously monitor and adjust the layout to maintain efficiency. To further enhance efficiency and stay competitive, warehouses can also embrace cutting-edge automation technologies. This is where AutoStore comes into play.
Embracing automation: The AutoStore solution
Designed for maximum efficiency, not random access
Digging is an intentional design choice that makes cube storage the most space-efficient, energy-saving, and scalable solution on the market. The result? A system that stores four times more goods in the same footprint compared to traditional storage methods.
Meet the pre-pick powerhouse — AutoStore’s dynamic top layer
AutoStore is designed for speed and optimised slotting. At any given time, AutoStore’s top layer holds the majority of goods ready for immediate picking — effectively creating one of the largest dynamic pre-pick buffers in warehouse automation.
- Access time? Seconds.
- Order fulfillment? Instant from the top layer.
- Need to “dig”? Rarely, if ever.
In a typical 20,000-Bin system with 16 levels, over 90% of picks come directly from the top layer — meaning the system is primed for high-speed fulfillment without any downtime. It takes about 28 seconds to retrieve is just 2.5 levels deep.
Sequencing like no other — a hidden superpower
AutoStore isn’t just fast. It’s strategic. While others chase direct access, it optimises order sequencing right from the top layer, ensuring the right products are ready in the right order. This level of dynamic control, known as “natural slotting,” is a game-changer for high-throughput operations.
What is ‘natural slotting’ what are the benefits?
AutoStore completely eliminates manual slotting by embracing three key assumptions:
- Inventory isn’t static — it’s highly dynamic, constantly growing and changing.
- Order demand is the strongest predictor for which Bins are needed.
- New inventory is inherently popular and can be placed on top of older inventory.
AutoStore performance is unaffected by how much product volume is stored inside the Grid or how the individual SKUs are arranged.
Bins used are returned and stored at the top layer of the Grid. Over time, slower moving Bins descend to the bottom of stack. This design philosophy ensures that only on rare occasions will Robots have to dig to the bottom of a stack.
Everything is placed into inventory and perfectly arranged by Robots, eliminating wasted time and labor resources and replacing them with a highly efficient automated system.
With that type of control over your inventory, why would you sacrifice storage density, energy efficiency, and intelligent sequencing just for random access to your inventory? You can’t, because in real-world operations, speed to fulfill orders — not random access — is what drives revenue.
In summary, the blend of advanced technology, real-time data optimisation, high-density storage, and scalability sets AutoStore apart as the future of warehouse slotting. It offers unparalleled efficiency, adaptability, and cost savings, making it an essential solution for modern warehouses aiming to stay competitive in a rapidly evolving logistics landscape.
Conclusion
Warehouse slotting is a critical component of efficient warehouse management. Get it right, and you’ll see increased picking efficiency, reduced labor costs, improved inventory accuracy, and enhanced space utilisation. Get it wrong, and your business is imperiled. Storing products randomly and relying solely on manual labor are common mistakes when it comes to slotting. But, by adopting best practices and leveraging advanced technologies, warehouses can optimise their strategies. AutoStore is intentionally designed around slotting because it’s a bedrock principle of inventory management. The system automatically arranges the most popular items at the top of the storage Grid to ensure that your most high-demand products are ready to ship in under 30 seconds. This “natural slotting” feature makes AutoStore ideal for warehouses that need fast fulfillment solutions.
Key takeaways
- Why storing inventory randomly is a nonstarter in warehousing.
- How slotting benefits your inventory management practices.
- Using historical sales data and order patterns to inform slotting decisions.
- Implementing ABC analysis to prioritize the placement of items based on demand frequency, size, and handling requirements.
- How AutoStore does it for you – learn the benefits of “natural slotting.”
Carlos Fernández, chief solutions officer, AutoStore